What is “RVDT”?
Rotary Variable Differential Transformer used for measuring angular displacement
April 20, 2021
RVDT, a type of electrical transformer is the leading product of Tamagawa Seiki Co., Ltd.
RVDTs perform to the best of their potential in harsh environment and widely used for position sensor in aircraft systems.
01. Basic Structure
The key to the long life is simple & metallic structure
Magnetic flux transmission between the Stator Core and the Rotor Core enables contactless measurement of angular displacement.
RVDTs need less number of piece parts and are mainly composed of metallic parts. This structure is the key to long life (MTBF) and perfectly suitable for aircraft applications which require high reliability and environmental resistance.
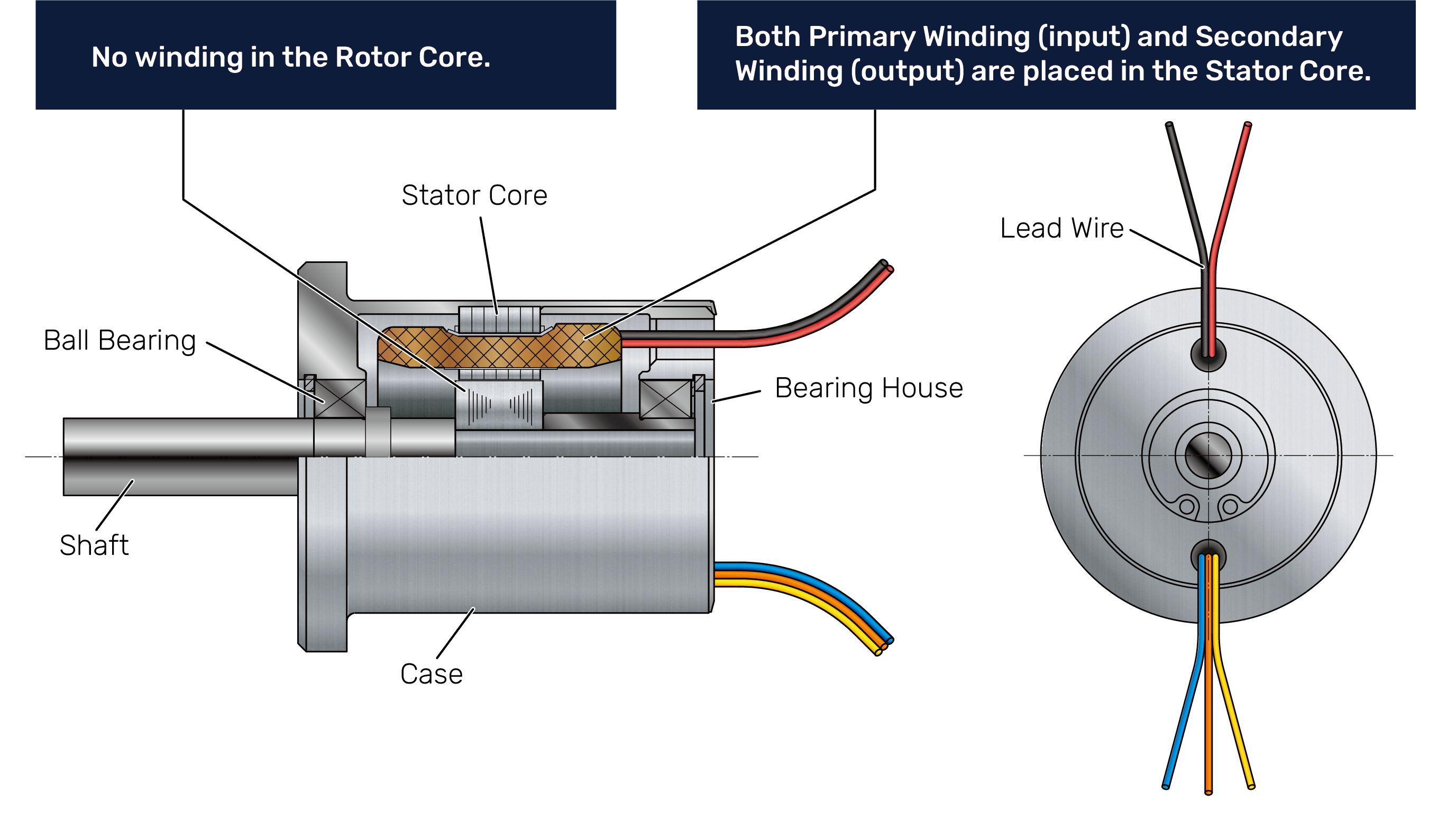
Roles of Primary Winding & Secondary Winding
RVDTs have five lead wires, two for input and three for output.

Primary Winding generates magnetic flux from excited alternating current (AC) voltage.

The magnetic flux generated in Primary Winding passes through the Rotor Core, and then passes through the two-phase Secondary Winding.

The Secondary Winding generates induced electromotive force and it depends on the magnetic flux passes through the Secondary Winding. RVDTs use this two-phase output; Va voltage / Vb voltage and measure angular displacement.
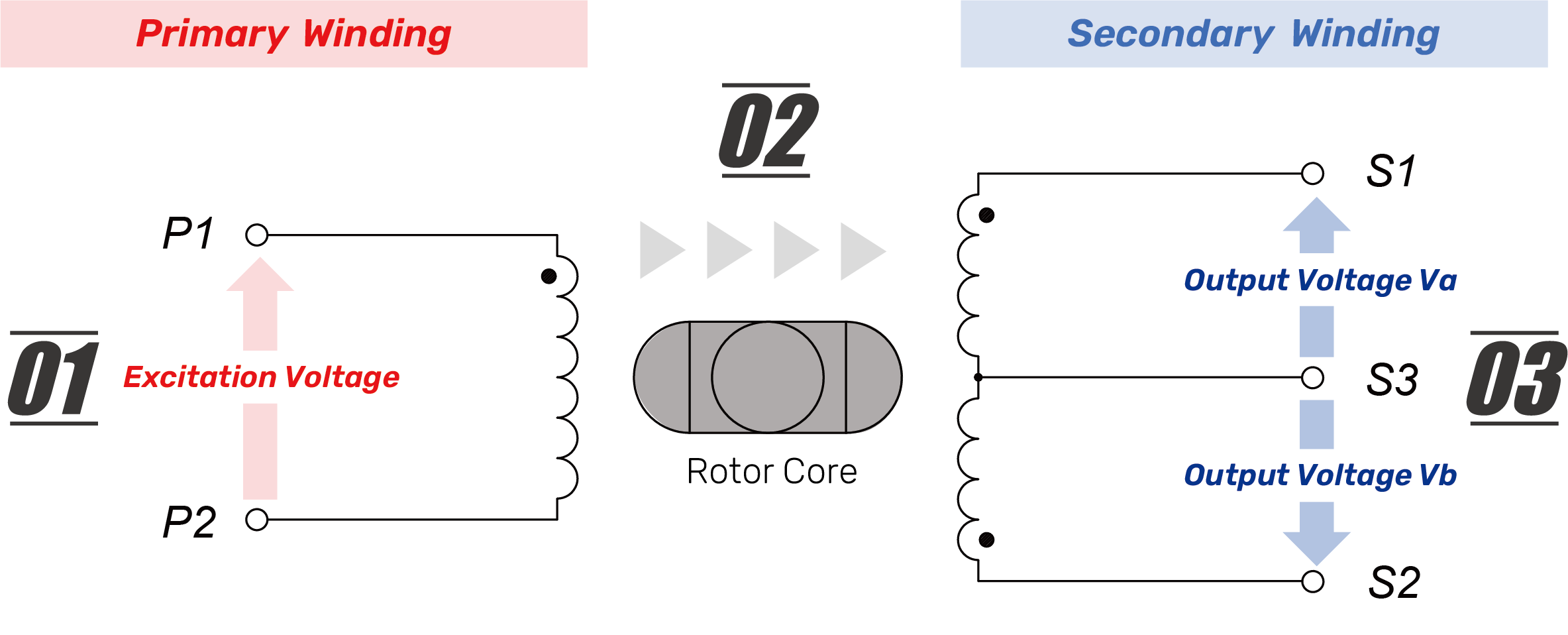
02. Failure Detection
Magnetic flux generated in Primary Coil circulates around the Stator Core and the Rotor Core. The change of the magnetic flux passes through two-phase Secondary Winding is depending on the angular displacement of the Rotor Core.
Electrical Zero Position
The Rotor position, which equally divides the magnetic flux in the Secondary Winding and generates same the voltage of both Va and Vb, is defined as Electrical Zero Position.
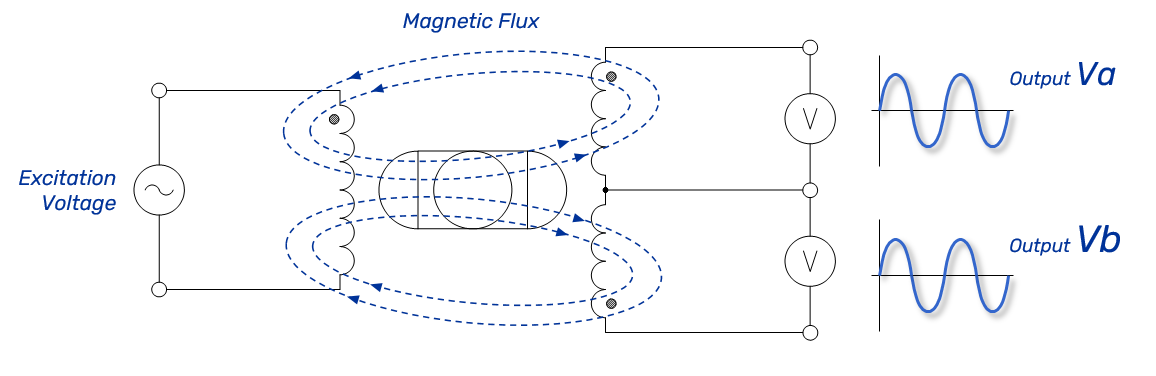
Rotor Rotation
Rotor rotation changes the magnetic flux flow, and then Va / Vb voltage increases and decreases. Va / Vb voltage symmetrically increases and decreases each other.
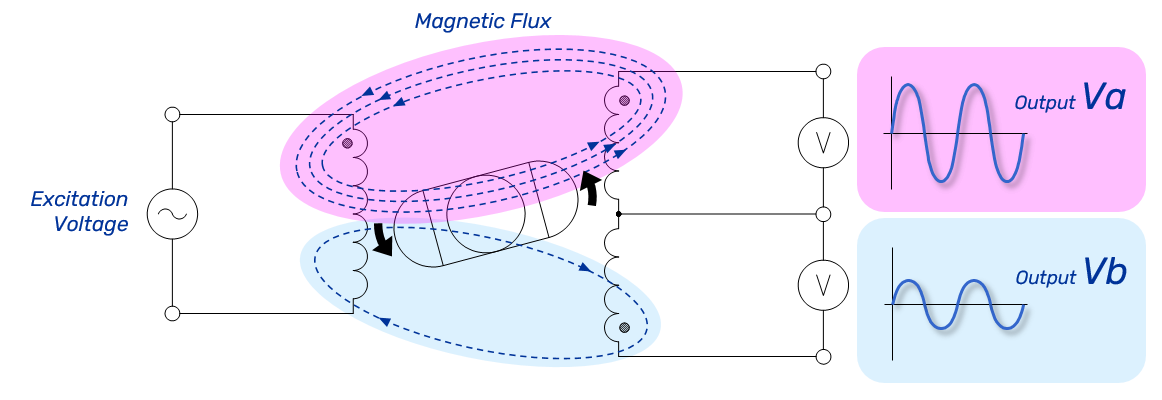
Works for “Failure Detection”
Va / Vb voltage increases and decreases in proportion to the Rotor rotation. Summation voltage (Va+ Vb) shows steady voltage which does not depend on Rotor rotation. This characteristic can be used for Failure Detection in a variety of systems loaded onto aircrafts.
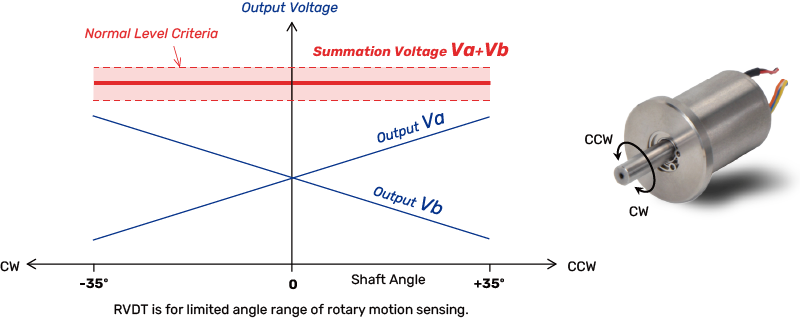
Failure Mode 1
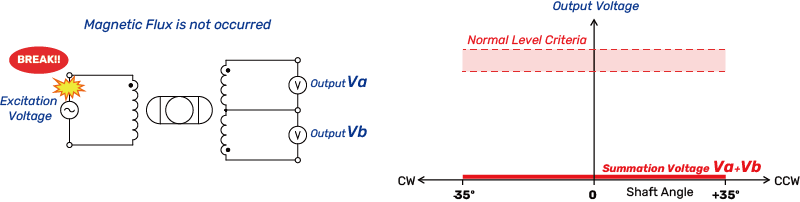
Failure Mode 2
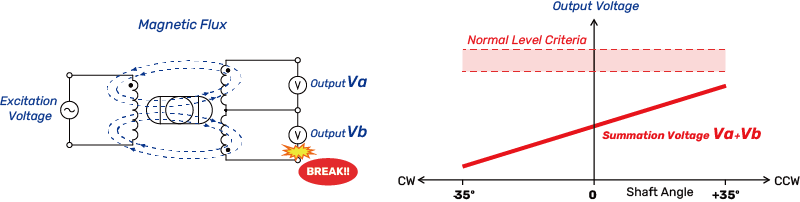
Aircrafts have various kinds of systems which use reciprocating movement in a limited angle, such as throttle levers, handles and pedals in Cockpit, and also flaps and spoilers outside of aircraft. For angle detection in these systems, RVDTs performs to the best of their potential.
Commercial Aircraft Applications
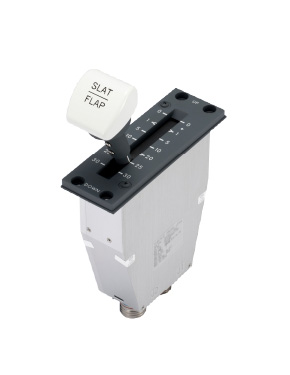
Flap / Slat Control Lever (FSCL)
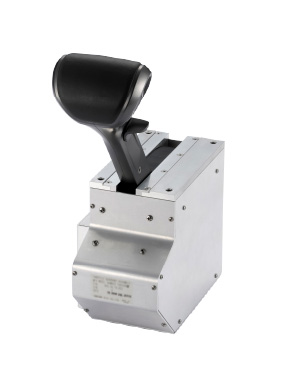
Throttle Quadrant Assembly
Single Lever
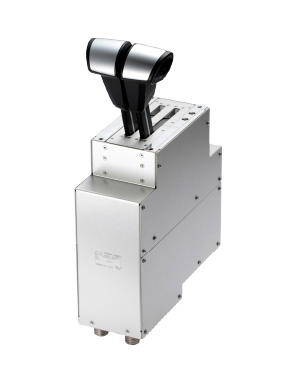
Throttle Quadrant Assembly
Double Lever
Tips for Engineers: Ratiometric Calculation
RVDTs are generally used for Ratiometric calculation based on the Va / Vb voltage. With this ratiometric calculation, the sensing function becomes stable by mitigating effects from ambient temperature and excitation voltage.
Ratiometric value is the output characteristic changing proportionately according to the Rotor rotation. Using this characteristic, angle position of RVDT shaft can be detected as electrical angle.
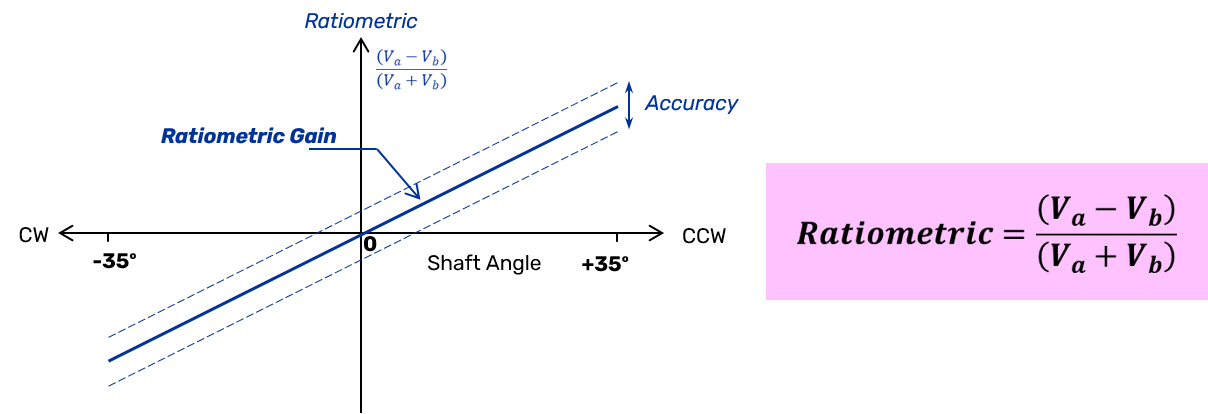
03. Production
Produce various kinds of RVDTs
Tamagawa has a production line at 2nd plant located in Iida City (Nagano Prefecture in Japan). All processes of assembly and ATP (Acceptance Test Procedure) can be completed at this facility.
Tamagawa’s own production engineering automates the winding process in accordance with RVDT designs. This automated winding technology is one of Tamagawa's key technologies.
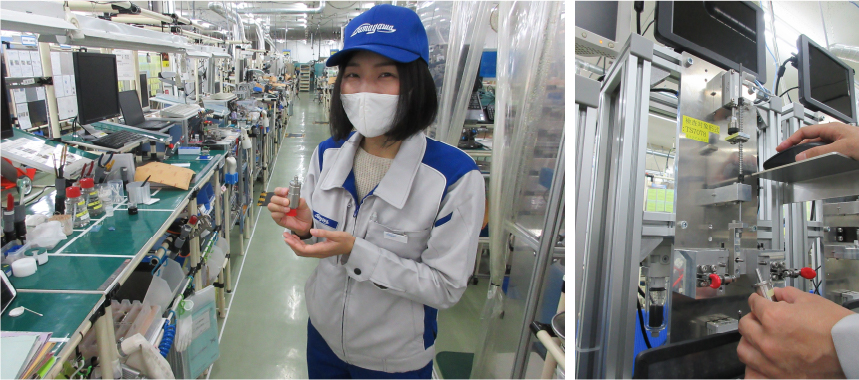
Don’t miss it!!
Introduction in next Newsletter
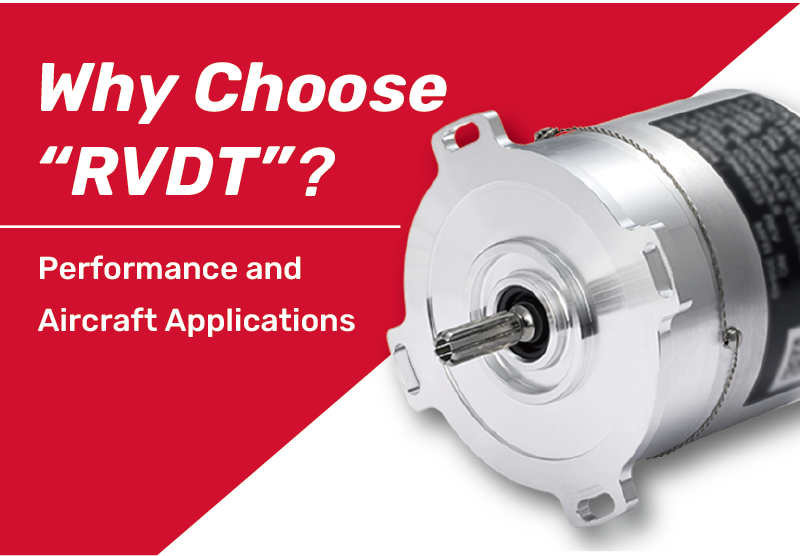
OUR TECHNOLOGIES
CAN HELP YOUR DEVELOPMENT
RVDT
Tamagawa RVDT provides linearly proportional voltages to the angular displacement with high reliability for vibration under extreme low/high temperature. Size 08, 10 and 11 are available in Tamagawa's RVDT series.
LVDT
Tamagawa LVDT is the standard linear position sensor for Flight control, Cockpit/Pilot control, EHSV (Electrohydraulic Servo Valve), Engine Valve applications, Fuel control and others.