Motor: Perfect Custom SolutionsAlways work and think together with customers
History of Tamagawa Motors has always been with our customers. Over 30 years, Tamagawa has continued research & development and acquired technical capabilities to satisfy customer's needs. For many years to come, Tamagawa supports and supplies perfect fitted Motors to customers.
01.Customized Motors for Aircraft
Motor with Brake + Sensor
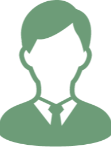
Customer's Request
“Motor with small Brake having higher vibration resistance at lower price… ”
- Brake - Optimize torque force vs spring force under higher gravity
- Low Price - Use in-house designed & manufactured Resolver
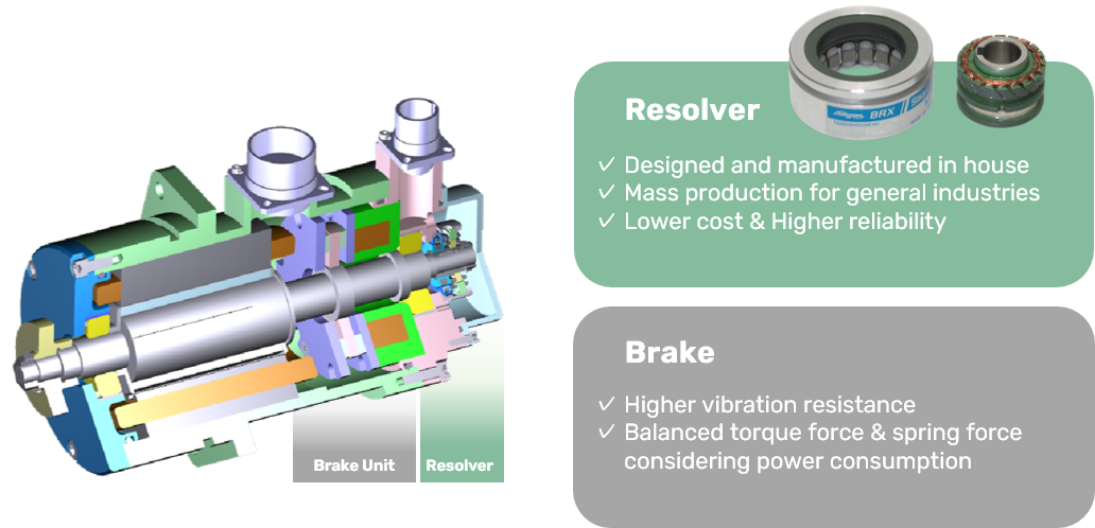
Similar Products:
Motor with Gear
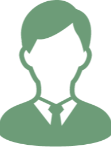
Customer's Request
“Compact space-saving Motor with enough torque at lower price… ”
Solution:
Design & Manufacture Gears in house to satisfy both technical requirements and lower price.
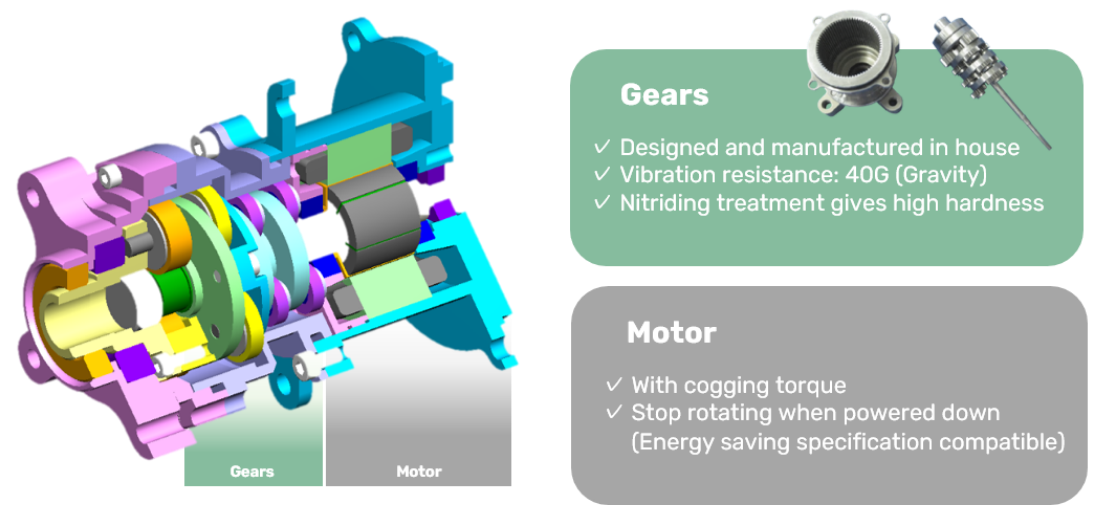
Similar Products:
02.A Story behind Developments
What is your biggest challenges in your life as a motor engineer?
At Tamagawa Seiki, more than 30% of employees engage in engineering and development. They work everyday for customers to find solutions and have a lot of stories with challenges and efforts.
For this interview, we have three engineers who is in charge of motors for Aerospace applications.
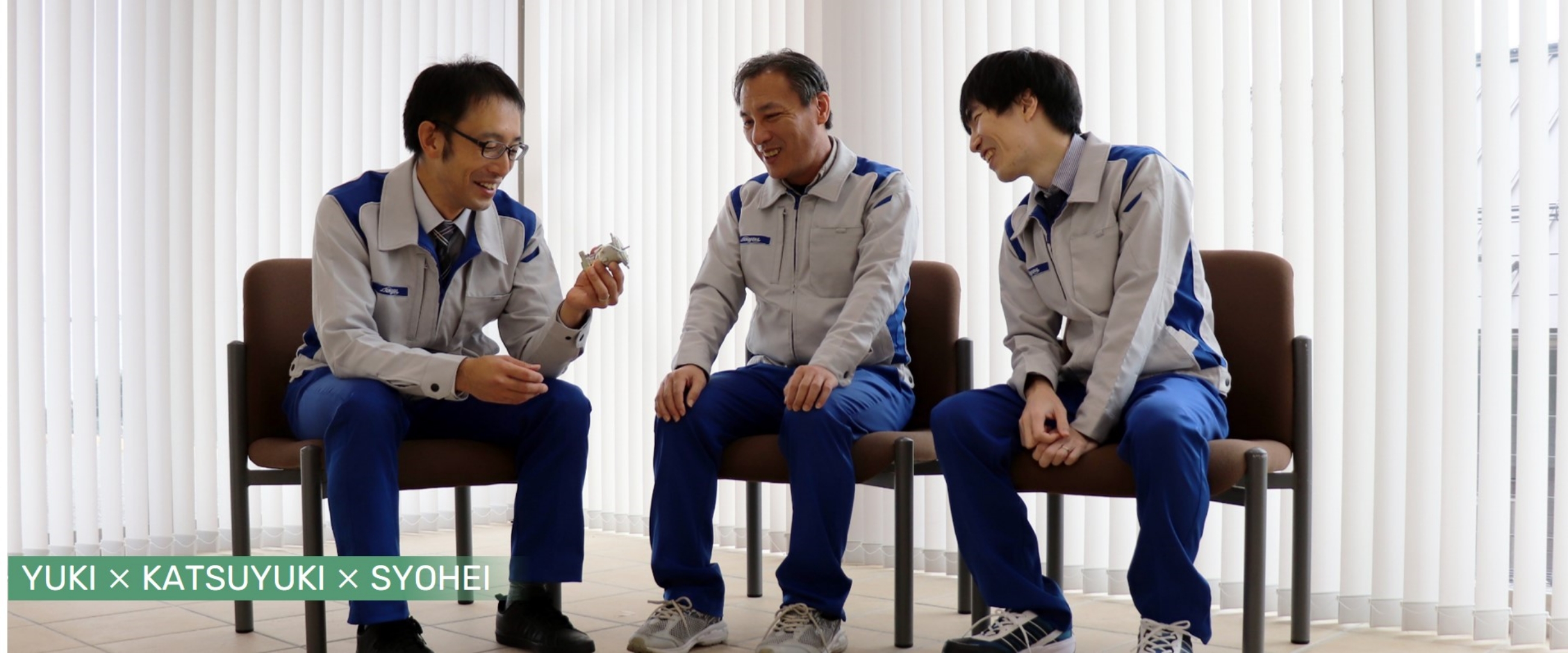
Unusual Requirements vs Unstoppable Motor
Katsuyuki : I will remember the development of a Stepper Motor with cogging torque forever, both in a positive and negative way. Our team proposed the concept to satisfy the customer and fortunately, won in a competition. At that time, it was an early stage of Aerospace business at Tamagawa and this win had greater meaning for all of us. But it was just the beginning of birth pains…
The customer requirements were more complicated than expected. When we delivered the first prototype to the customer, we received complaint about it’s coasting. It was totally unexpected! For power saving, the customer’s system was actually designed not to apply an electrical current to our Stepper Motor in a resting state. This was completely new to us because Stepper Motor is generally used with an electrical current applied at all times. As a result of this, we were in a desperate need of reconsidering the whole design of the rotor and stator to meet requirements both in operating state and resting state.
Syohei : This is a famous story in our team that you worked not only on Christmas holiday but also on New Year holiday and completed the redesign of the rotor and stator only in a month.

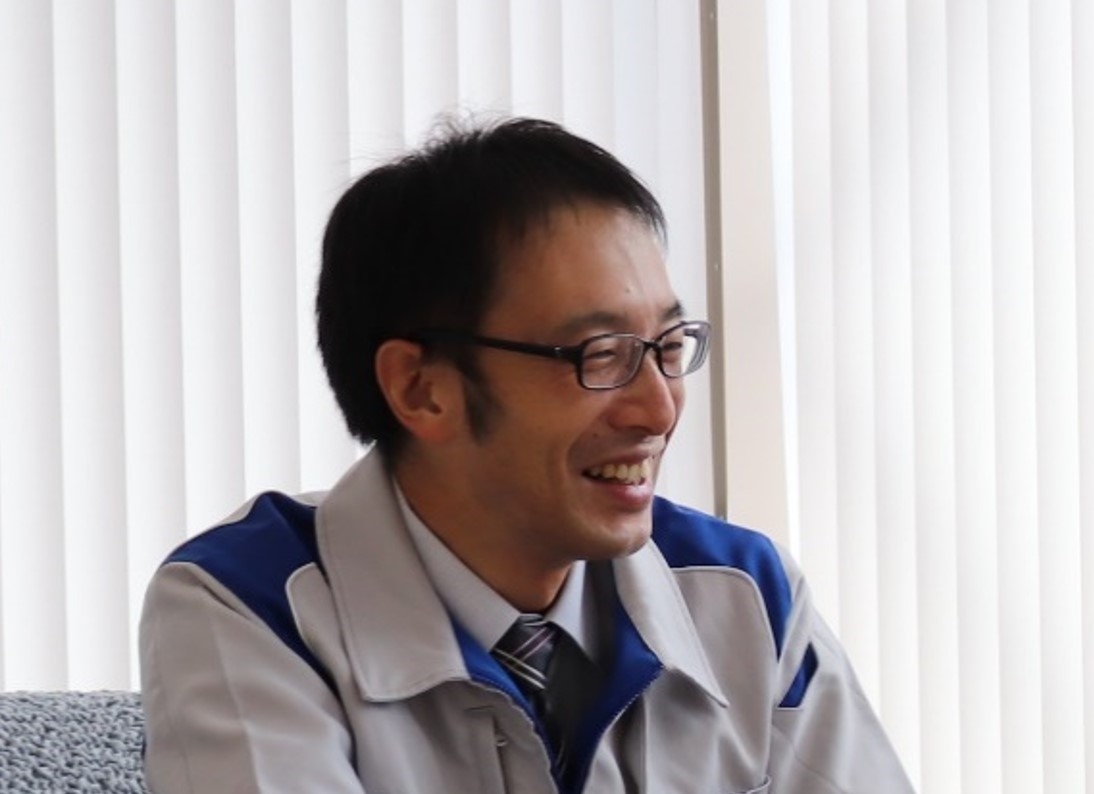
Drastic increase in Manufacturing Cost
Yuki : This project is unforgettable for me too as we did also design and manufacture the gears of this Motor. At the beginning of this project, we had supplier who can manufacture the gears. However, due to the repeated specification changes, we were facing drastic increase in manufacturing cost. We tried to reduce the cost and requested the supplier for price reduction, but it was refused. Then we had no other choice to handle the design and manufacture of the gears by ourselves.
Although the gears were supposed to be cut by the equipment of direct-cutting at supplier’s facility, there was no such hundreds of millions (yen) of equipment at Tamagawa. The way we found to overcome this situation is material change. We made multiple samples and tried some special processes to harden the material. This was a big challenge with uncertainty and it was a huge pleasure when finally found solution to satisfy our customer’s requirements.
However, after the success in the design and production of the gears, we heard that this change caused our customer’s customer so much trouble. That is because, our material change required them to perform additional qualification tests. It’s another long story, I will stop talking about it…
Overcome Failure at Qualification Test
Syohei : I know this Motor had a higher vibration requirement, 40G (Gravity). It was huge! As the level of requirement from DO-160G is under 20G and I have never seen such a requirement!
Katsuyuki : Me neither. The first prototype didn’t have enough endurance for 40G and were came to pieces during the vibration test. We solved this issue by welding after press-fitting and this made the Motor more robust.
Yuki : This Stepper Motor has a long long history with blood sweat and tears. However, it is now one of the flagship products in Aircraft lineup at Tamagawa and used in a lot of Aircrafts without any problem for more than 10 years.
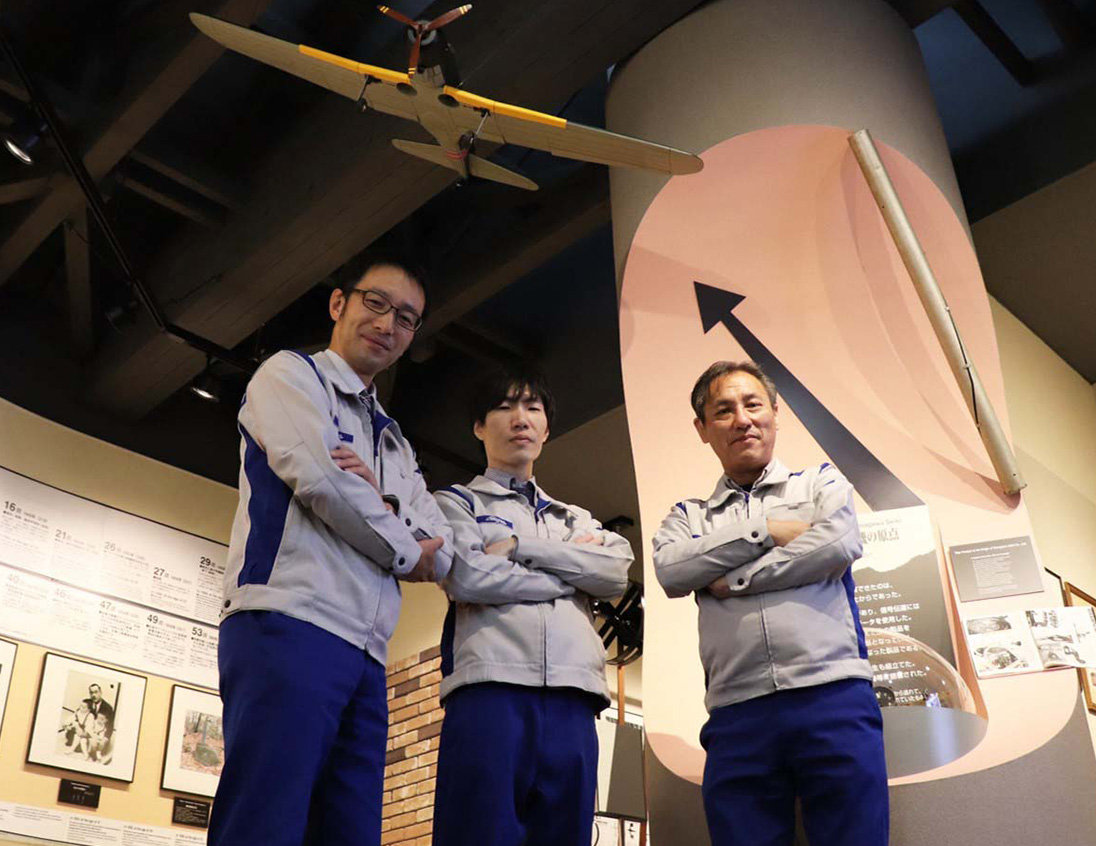
OUR TECHNOLOGIES
CAN HELP YOUR DEVELOPMENT
RVDT Cluster
TAMAGAWA RVDT Cluster with integrated gears is angular position sensor unit, equipped with maximum 5 RVDTs in the shell to realize redundancy.
Resolver with Gearbox
Gearbox for Resolver is available for reduction and acceleration. TAMAGAWA offers custom designed resolver with spur gear and planetary gear.