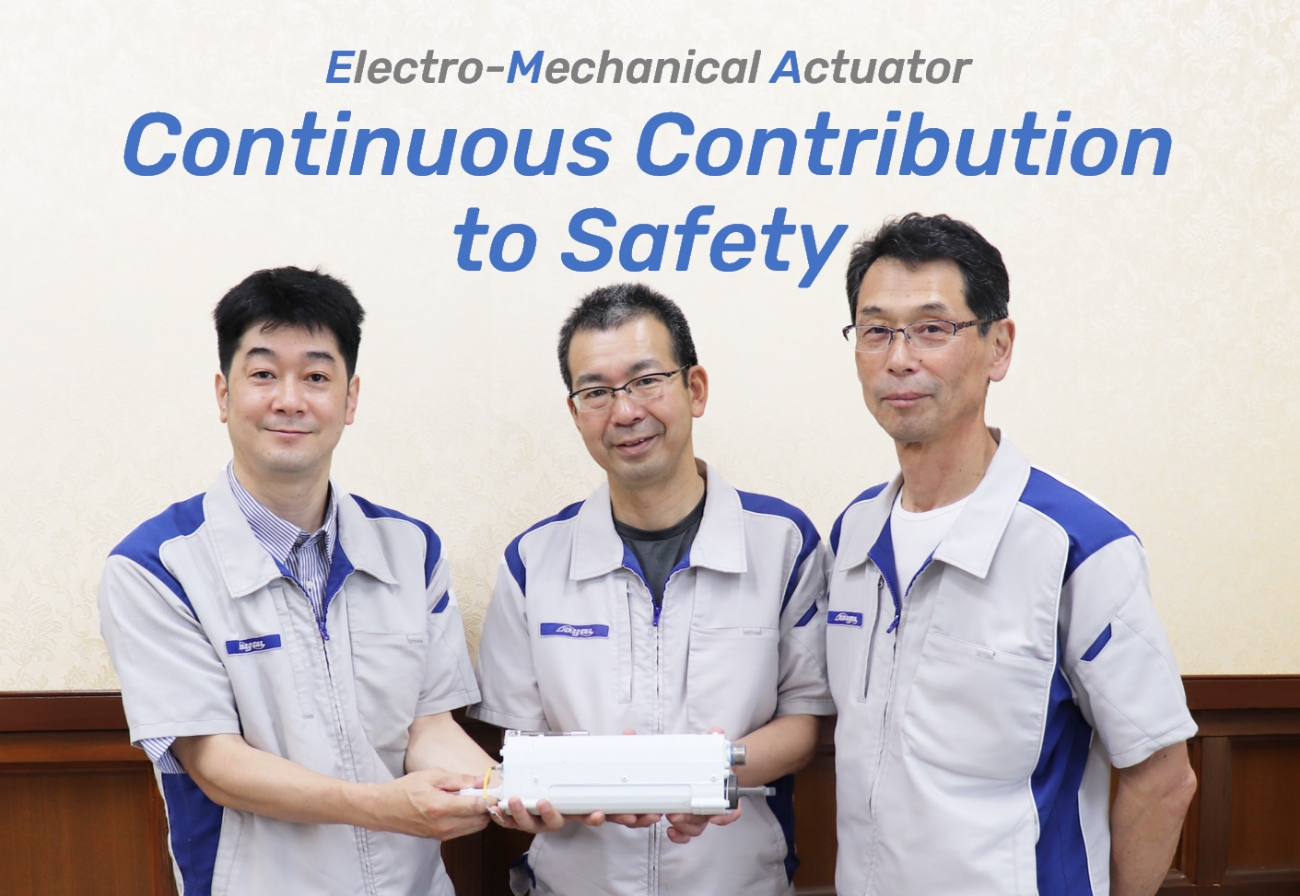
Always living up to high expectations of customers
Electro-Mechanical Actuator is one of Tamagawa Seiki’s advanced products incorporating customers’ growing needs for safety.
We will show you a part of our detailed design for Actuator and behind the scenes of the developments.
01.Design for Reliability
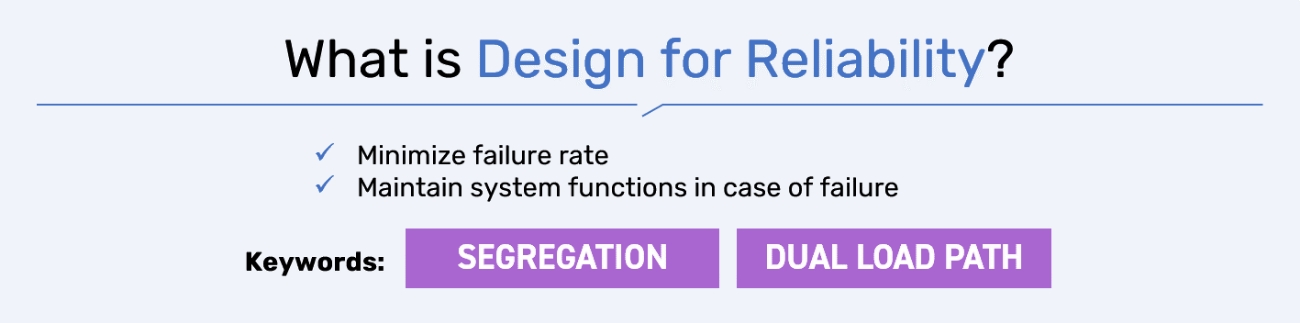
Segregation - Rudder Trim Actuator
Even if one sensor fails, Tamagawa Actuator maintains the functions:
- Separate the Command Lane (COM) and the Monitor Lane (MON)
- Make the Stroke Detection redundant - LVDT x 4ea
- Separate the structure by systems, without any interference each other - Drive system, COM Stroke Detection and MON Stroke Detection
Dual Load Path - Trim Tab Actuator
In case the Actuator breaks, Tab control surface lost and the aircraft will be in critical condition.
Even if one Load Path breaks, Tamagawa Actuator maintains the function using another Load Path:
- Make the Rods for linear actuation redundant
- Make the Load Path of Tab control surface and Main control surface redundant
02.A Story behind Developments
Actuator engineers are required not only a huge amount of work for design, analysis, tests and documentation but also a great deal of experience and more advanced skills for design.
For this interview, we have three Actuator engineers representing Tamagawa, including a head of engineering.
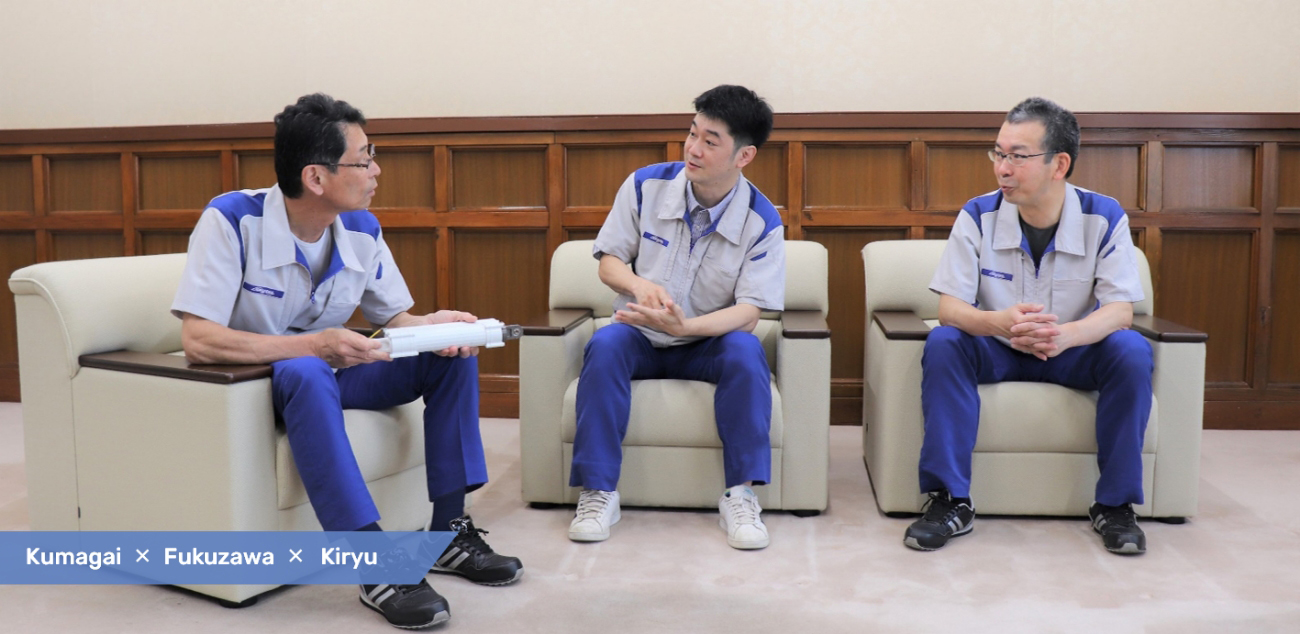
What was the biggest CHALLENGES you've ever had in developing new Electro-Mechanical Actuators?
Very “First” Development | Landing Gear Actuator
Kumagai : After all, I think Tamagawa’s very first development of Electro-Mechanical Landing Gear Actuator for Aircraft was the most challenging one for me. We had experience in developing EMA for military program but never for commercial aircraft. I was assigned to the Project Manager and set up a dedicated project team bringing 7 engineers to develop 7 types of EMAs.
Fukuzawa : I remember much about this project! That’s because, we developed Freefall Mechanism at this time - which became the basis of Tamagawa LGA designs going forward.
Kumagai : That’s right. Our customer eagerly said FREEFALL but I was clueless about it. You know, we didn’t have any experience in Electro-Mechanical LGA then. Of course, I knew the mechanism of hydraulic actuator – deploys the landing gear into the down position when removes oil from the actuator - but what we needed to develop was electric mechanism pulling the landing gear down and deploying it.
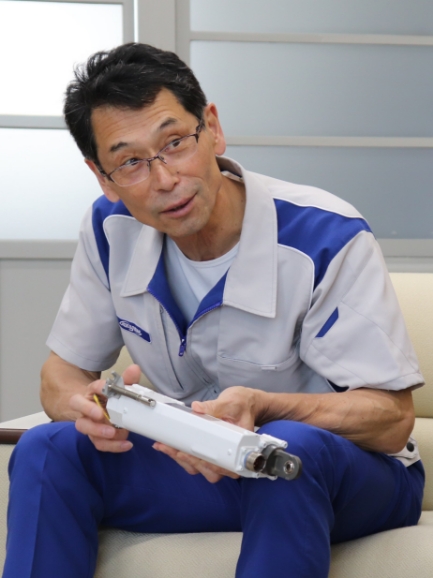
Fukuzawa : I know you dedicated yourself completely to the development of Freefall Mechanism all day everyday.
Kumagai : I usually had a web meeting with customers very early in the morning and then repeatedly made the prototypes until mid night. And after the date was changed, I often received phone calls from the customer - they wanted to confirm the progress... It was tough but this mechanism is still the key function of Tamagawa LGA, I feel my efforts paid off.
Fukuzawa : We had difficulty passing the Icing test as a Qualification test.
Kumagai : Right after the first test, we found the mounting screw was fallen off from the Actuator. We tried again but the result was the same. Both results were the same and we concluded the screw became loose during the test. It was totally unexpected.
Fukuzawa : This unexpected failure was the background of the birth of Drain Hole. Tamagawa LGAs have this design since then.
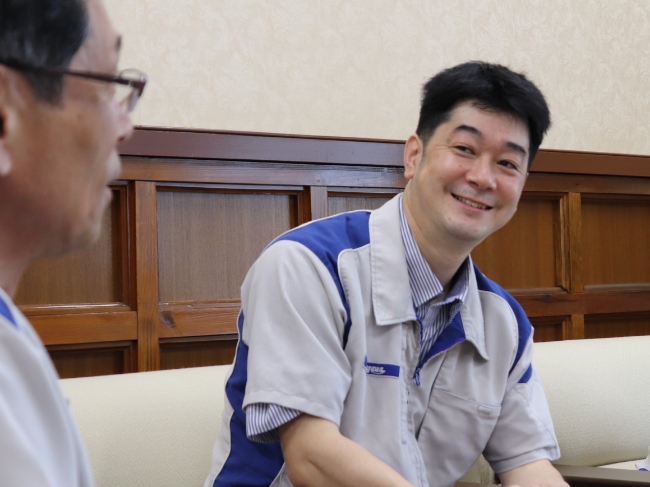
Kumagai : The Icing test was required to be performed in low pressure. This condition made moisture flowed into the screw and frozen, and then loosen the screw and fallen off from the Actuator. This was the cause of this issue. So I re-designed the screw adding a hole on it so as to let air out from the screw. This design successfully stopped moisture staying in the screw. I was so relieved that Actuator finally passed the third trial. Because our team visited US three times for this test...
Fukuzawa : It never ends if we talk about this first development. We were in difficulty understanding the Over the Center mechanism, and also the One Way Clutch mechanism... But all in all, Freefall Mechanism is the toughest challenge for us.
Kumagai : Why didn’t I apply for a patent about this mechanism...!
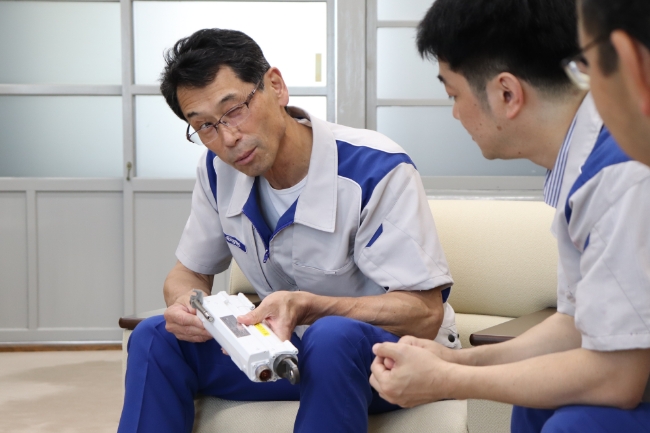
What was the biggest BENEFITS you've ever had through the new development of Electro-Mechanical Actuators?
Essence of “Segregation” | Rudder Trim Actuator
Kiryu : The first one came to my mind is the development of Rudder Trim Actuator. It was the most complicated Actuator in my experience.
Kumagai : I remember we visited customer and stayed at their office during summer vacation and winter vacation for this development. It took so long to fix final configuration.
Kiryu : What we struggled was to understand “design for reliability” that was requested by customer. We changed the design of the Actuator again and again so as to form the ideal configuration with segregation. This was the core requirement that was strongly expected by customer.
Kumagai : It was the first time we faced such requirements. It was hard for us to visualize what they exactly expected!
Kiryu : Eventually, the Actuator had 8th layer circuit boards and integrated 2 types of LVDTs to achieve the segregated configuration.
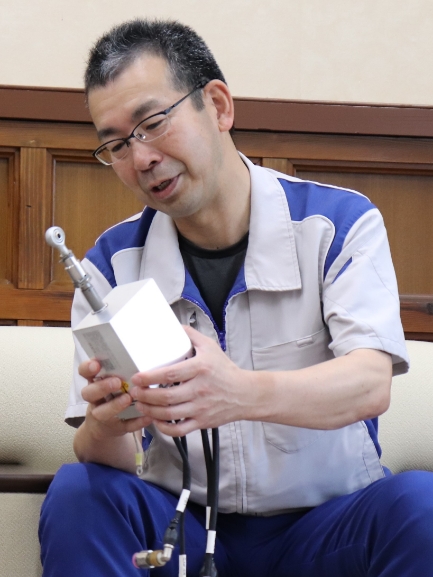
Kumagai : I’ve never seen an Actuator having such a complicated structure.
Kiryu : It is a rough explanation - the final configuration of the Actuator is like a small box with numerous earthworm’s holes, about 8 mm each. We were requested to segregate the wire harness completely and the holes were needed for such structure, I mean for segregation.
Kumagai : The key to this development was how to break down and understand the “essence” of design for reliability. It seemed to me that the customer was also struggling to understand the requirement of segregation from their customer.
Kiryu : The philosophy of segregation was not so permeated into the aerospace industry in those days. We got through a difficult time and learned a lot about the philosophy of segregation, for both structure and signal. In the sense that we learned a new philosophy at an early stage, I think we obtained maximum benefit from this development.
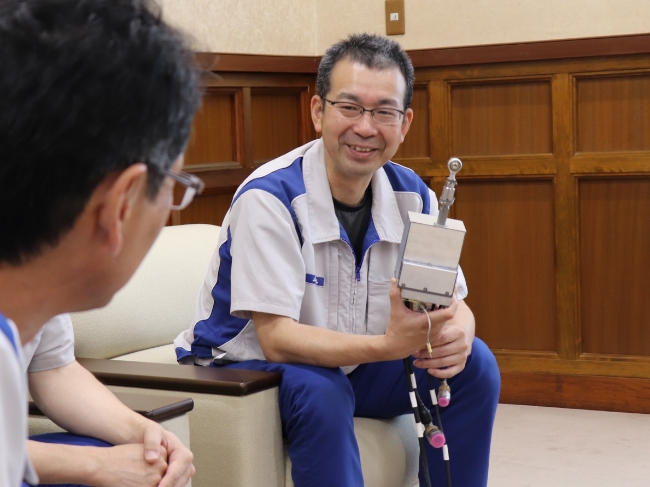
Perfect Redundancy of “Every Single” Parts | Trim Tab Actuator
Fukuzawa : I also had a hard time with “Design for Reliability”. An Actuator I designed was required to have such structure - make redundant of all the Load Paths.
Kiryu : It is called “Dual Load Path”.
Fukuzawa : Absolutely. It means all the routes starting from the input of Actuator to the output shaft to the airframe shall be duplicated. In case a part of Actuator breaks, the Actuator maintain the functions - that was the design we were requested.
Kiryu : The design philosophy of Dual Load Path was also new to us at this time.
Fukuzawa : Yes, it took a lot of time to fully understood what they expect. I had a series of discussions with customer and made many design changes, and finally fixed the current configuration with duplicated load paths.
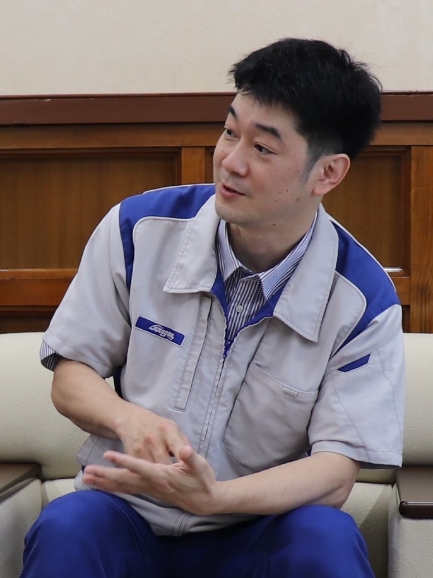
Kiryu : I remember we had trouble performing Qualification Test - due to this Dual Load Path.
Fukuzawa : We needed to pass the Fatigue test as Customer said this test was very important for this Actuator. Through multiple stages of design changes, I felt confident in passing the test. But I found the Actuator was in a need of evaluating each shafts separately - due to this redundant configuration.
Kiryu : So, it took much more time and cost than we initially expected!
Fukuzawa : This experience became an important lesson for me. For now, Design for Reliability is getting established as a general philosophy in the aerospace industry, and I can make use of my past experiences to new developments. Our team have accumulated lessons learned and is passing it on to the younger generation.
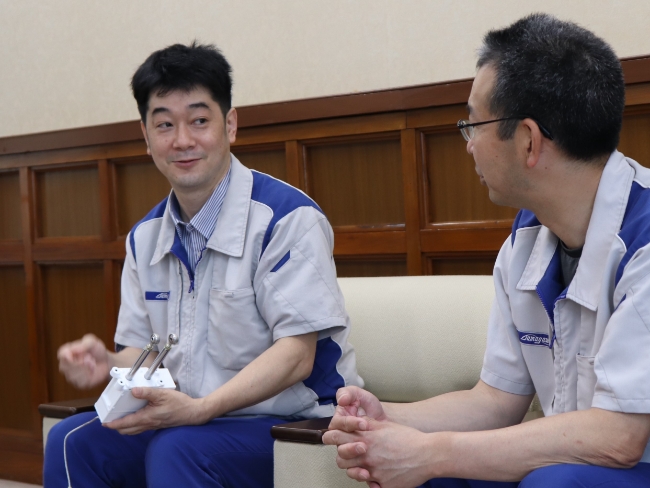
Kumagai : New developments are certainly challenging but we learned something new every single time. As time goes by, I think the performance expected to EMA is becoming more sophisticated. Always living up to higher expectations from customers, I believe we can expand the active filed of Tamagawa EMA even further.
Kiryu : Thanks to our Customers who always give us new challenges, Tamagawa has been a frontrunner as an EMA manufacturer for aircraft. All of the hardships we have gone through are now being applied as know-how to the aircrafts flying in the sky at this moment.
Fukuzawa : We are also confident in the fact that our Actuator has a rare occurrence of failure. As a manufacturer and engineer, my greatest desire is to contribute to aviation safety. We would like to continue to evolve so that people will say "Tamagawa for reliable EMA”.
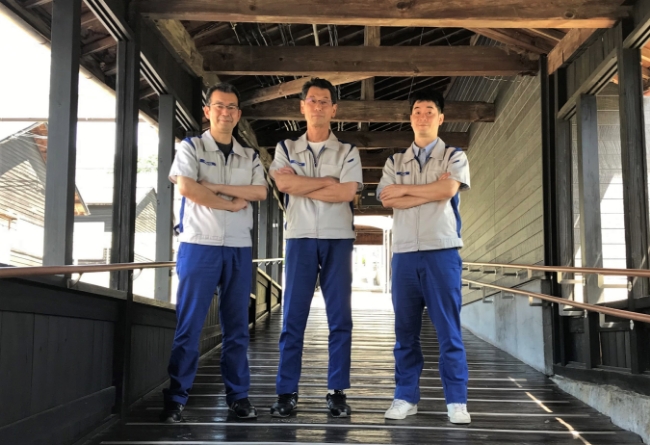
OUR TECHNOLOGIES
CAN HELP YOUR DEVELOPMENT
LVDT
Tamagawa LVDT is the standard linear position sensor for Flight control, Cockpit/Pilot control, EHSV (Electrohydraulic Servo Valve), Engine Valve applications, Fuel control and others.
Brushless DC Motor + Brake + Sensor
This type of Tamagawa Motor integrates electric brake and feedback angular sensor like Hall IC or Resolver. Typical applications are for power drive unit and actuation and motion control systems.